Concrete Repair Dallas offers warranties and insurance to cover their work. They also have the training and safety equipment to complete repairs safely and effectively.
A good bond between the repair material and the existing concrete requires a proper scratch coat. It is made by mixing the repair product with water until it reaches a soupy consistency.
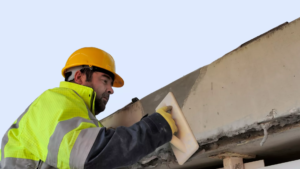
When commercial concrete surfaces crack, it’s unsightly and can reflect poorly on the business. That’s why addressing cracked concrete is so important. With the right repairs, cracks can be minimized or eliminated.
Various materials can be used to repair concrete surfaces, but each material has its advantages and disadvantages. When deciding which product to use, it is important to consider the physical properties and durability of the material, the method of application and curing, and the environmental and cost impact.
Concrete surface cracks can be caused by a number of factors, including weather conditions and ground movement. To address these issues, commercial property owners should have a well-planned maintenance strategy in place to inspect and repair concrete surfaces as they become damaged.
For small imperfections, such as surface cracks, a concrete patching compound is a simple solution. These compounds are typically composed of cement and masonry sand mixed with water. They can be purchased at most home improvement stores and are relatively inexpensive. When using this product, the repair area should be thoroughly cleaned and brushed to remove any loose debris. Then, the product is applied with a mason’s trowel or putty knife and pressed down firmly to eliminate air pockets. It is then smoothed and leveled with the surrounding concrete.
Another option for repairing surface cracks is an epoxy or latex repair product. This type of product is often available in a wide range of colors to match the existing concrete surface and can be purchased at most home improvement stores. As with the mortar mix, the repair area should be thoroughly cleaned and blow or swept to remove any loose debris. If the area is exposed to the elements, it should be covered with plastic sheeting until it is dry.
For wide cracks, foam backer rod may be placed in the crack to provide support. A mortar or epoxy mix may be then used to fill the crack and level it with the surrounding concrete. It is important to note that cracks caused by expansive soil movements should not be filled with this type of product as it may cause further damage.
Repairing Leaks
Leaking concrete cracks can cause serious problems in a home. They can ruin carpets and furniture, encourage mildew and mold, and substantially increase water bills. Depending on the extent of the leak, you may need to have the entire slab replaced. A slab leak can be very difficult to detect, but is absolutely essential to fix as quickly as possible. Slab leak repair should be done by a professional plumbing company.
Injection materials are the preferred method for sealing concrete foundation cracks that are actively leaking. Hydra Stop 300 polyurethane foams on contact with water and expands inside the crack to seal out the leak. The injection process is simple, non-invasive, and quick. For larger repairs, a liquid bonding material can be applied to the concrete surface and allowed to dry until it is tacky. Then, the concrete crack injection material can be applied as directed.
If a crack is not active and does not require immediate attention, a hydraulic cement or crystalline system can be used to halt the leak temporarily. However, this is not an effective long-term solution. If moisture migration is left unresolved, it will continue, exposing the reinforcing steel to further corrosion in adjacent passive areas.
Traditional patch repair of corroding areas may arrest the problem, but it cannot solve the root cause of the corrosion, which is most likely chloride contamination (see Figure 43). In these circumstances, an appropriate repair strategy should include the use of discrete sacrificial anodes to limit corrosion in the adjacent concrete.
Whether you are repairing a cracked floor or a slab under your house, the most important thing to remember is that prevention is much easier than cure. Identifying and completing a slab leak repair before it causes major damage to your home will save you money, time, and headaches down the road. If you suspect that you have a slab leak, speak with your plumbing company and an insurance agent. Insurance companies usually only cover sudden and catastrophic damages, and are reluctant to pay for the gradual and often ignored damage that results from slow water infiltration.
Reinforcing Concrete
Concrete repair often involves increasing the strength of the existing concrete. This is done by replacing the existing concrete aggregate with higher-strength materials or by adding steel reinforcing bars to create a stronger mix.
In general, the stronger the concrete is, the more durable it will be. However, the exact amount of reinforcement needed depends on the environment in which the concrete will be used and the type of load it will be subjected to. For example, high-strength, high-E-modulus concrete is generally used in floors and foundations that will be exposed to heavy traffic or loading. It is also typically used in structures that must withstand a large amount of movement, such as bridges and elevated roadways.
A proper concrete restoration design requires a thorough evaluation of the structure and its components to identify the most beneficial method of strengthening. This includes a careful inspection of cracks, which are commonly observed in concrete as they develop during the curing process. Some types of cracks may be attributed to plastic settlement, while others are the result of corrosion of steel reinforcement or other factors that can negatively impact structural integrity.
The best way to strengthen concrete is by placing steel rebar in the form of wire mesh or by using steel fibers, which are woven into a polymer matrix and electrically welded together at intersections. This reinforces the existing concrete and increases its tensile strength, while also reducing permeability and freezing-thawing resistance.
Choosing the right concrete repair material is also important. It must be compatible with the quality of the existing concrete, as well as able to meet the project requirements and in-place service conditions. Incompatibility between the repair material and the existing concrete can cause premature failure of the repaired structure. This can occur due to different thermal expansion or shrinkage, different chemical reactivity, or differences in the physicochemical properties of the interface zone (zone of 1-2 mm thickness) between the repair material and the host concrete.
In addition to the selection of an appropriate repair material, it is important to follow good construction practices. This includes a thorough site cleanup, adequate surface preparation, and good curing techniques. In addition, a comprehensive testing program is required to monitor the performance of the repaired structure and ensure that it meets its required function.
Repairing Structural Damage
Structural damage is much more serious than simple cracks, and can involve significant concrete movement, structural deterioration or even collapse. Such a problem is best diagnosed by a registered professional engineer, and usually involves a thorough inspection that can reveal the scope of repairs to be required. Structural damage repair often involves extensive shoring, rebar placement and concrete replacement, and it is important to follow an experienced engineer’s recommendations to the letter.
Generally, the type of concrete repair material selected should be compatible with the quality of the existing concrete and the construction methods used. It is also important to consider the durability of the concrete repair material and its impact on the existing concrete, including freeze-thaw durability. Additionally, the quality of the surface preparation and curing conditions are very important in achieving durable concrete repair.
Some types of deterioration in concrete can be arrested or delayed without the need for major repair. If the damage affects the safety or serviceability of a structure, however, it is prudent to have the structure repaired as soon as possible to prevent further deterioration and eventual failure.
A visual examination, a delamination survey, or potential mapping may be sufficient to determine the severity of the concrete damage and the extent of repairs required. In many cases, it is necessary to chip away some of the damaged concrete to assess the condition of the reinforcing steel and the depth of deterioration in the concrete. This is particularly true for chloride-induced deterioration of concrete, where the corrosive action may not be seen until the concrete is chipped open.
Once the concrete has been successfully repaired, it is very important that adequate care be taken to ensure that the repairs are properly cured and tested. The use of a suitable curing regime is essential to the success of the repair and to ensuring that the repaired concrete achieves its intended strength and durability. Depending on the repair materials, it may be necessary to provide a suitable wet curing environment for the repair to succeed. Failure to do so will result in the repair being prematurely deteriorated and will require further costly repairs.